The Process and Benefits of Automotive Lighting Annealing Ovens
Automotive lighting components, such as headlights, taillights, and indicator lights, require high durability, precision, and clarity to meet industry standards. One of the critical steps in their manufacturing process is annealing, which enhances the strength and longevity of these components. Annealing ovens play a vital role in ensuring that automotive lighting parts can withstand temperature fluctuations, environmental stress, and long-term usage without compromising performance. This article explores the annealing process in automotive lighting manufacturing and the benefits of using annealing ovens in production.
1. Understanding the Annealing Process
Annealing is a heat treatment process that involves heating a material to a specific temperature and then cooling it at a controlled rate. This process helps relieve internal stresses, improve mechanical properties, and enhance material durability. In automotive lighting, annealing is primarily used for:
Glass components (e.g., headlamp lenses, covers) to improve strength and reduce brittleness.
Plastic components (e.g., polycarbonate lenses, housings) to remove stress from the injection molding process.
Metal parts (e.g., reflectors, brackets) to enhance ductility and prevent cracking.
2. How Automotive Lighting Annealing Ovens Work
Annealing ovens are designed to provide precise temperature control and a uniform heating environment to optimize material properties. The key steps in the annealing process include:
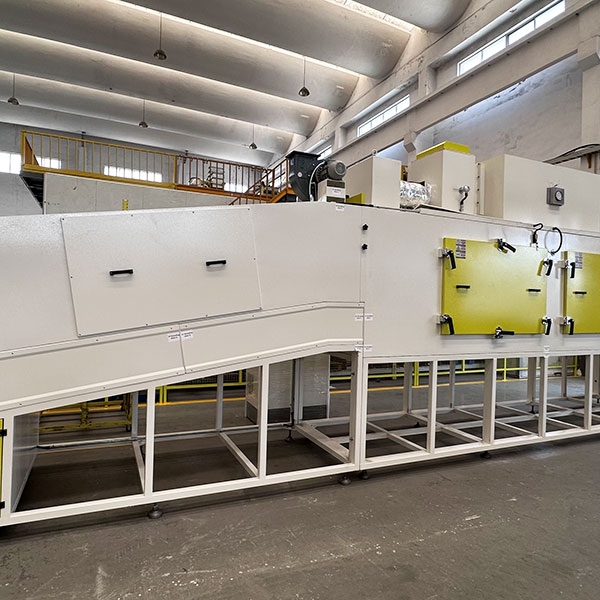
a) Preheating Stage
► The oven gradually heats the components to a pre-defined temperature.
► For glass components, temperatures range between 500-600°C.
► For plastics, annealing occurs at 80-130°C, depending on the material type.
The heating process is carefully controlled to prevent sudden temperature changes that could lead to material stress.
b) Soaking Stage
The components remain at the target temperature for a specific period to allow internal stresses to dissipate.
► The soaking time varies based on material thickness and composition.
► Precision monitoring systems ensure even heat distribution across all components.
c) Controlled Cooling Stage
The components are cooled slowly in a controlled manner to prevent thermal shock and warping.
► Cooling rates are adjusted to maintain dimensional stability and prevent defects.
► Advanced cooling systems use air or water cooling techniques to optimize the process.
3. Features of Modern Automotive Lighting Annealing Ovens
a) Automated Temperature Regulation
► Digital controls and real-time monitoring sensors adjust heat levels automatically to ensure consistent results.
► Temperature profiles can be customized for different materials, ensuring optimal treatment conditions.
b) High-Precision Heating Elements
► Modern annealing ovens use infrared, convection, or induction heating to provide efficient and uniform heat distribution.
► Smart heat management systems prevent overheating and energy loss.
c) Advanced Insulation Technology
► High-quality thermal insulation materials help retain heat, reducing energy consumption and maintaining a stable internal temperature.
► This leads to increased cost efficiency and sustainability in manufacturing.
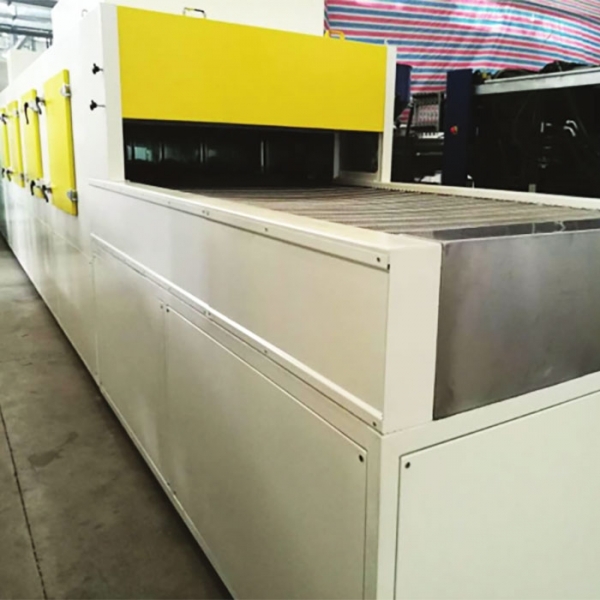
d) Modular and Scalable Design
► Many state-of-the-art annealing ovens feature a modular design, allowing manufacturers to scale operations based on production volume.
► Custom configurations enable adaptation for different lighting component sizes and materials.
4. Benefits of Using Automotive Lighting Annealing Ovens
a) Improved Material Strength and Durability
Annealing strengthens glass and plastic materials, making them more resistant to impact, thermal stress, and environmental conditions. This is crucial for automotive lighting components that must withstand temperature variations, vibrations, and external forces.
b) Reduction of Internal Stresses
During manufacturing, processes such as injection molding and extrusion create internal stresses in plastic and glass components. Annealing eliminates these stresses, preventing issues like cracking, warping, or premature failure.
c) Enhanced Optical Clarity
For polycarbonate and glass lenses, annealing reduces internal distortions, improving light transmission and uniformity. This enhances the overall brightness, beam quality, and visibility of automotive lighting systems.
d) Consistent Product Quality
Automotive lighting annealing ovens ensure uniform heating and cooling, leading to consistent product properties across different batches. This is essential for maintaining strict industry standards and regulatory compliance.
e) Energy Efficiency and Cost Savings
Modern annealing ovens are equipped with advanced thermal insulation, automated controls, and energy-efficient heating elements. This results in lower energy consumption, reduced operational costs, and a more sustainable manufacturing process.
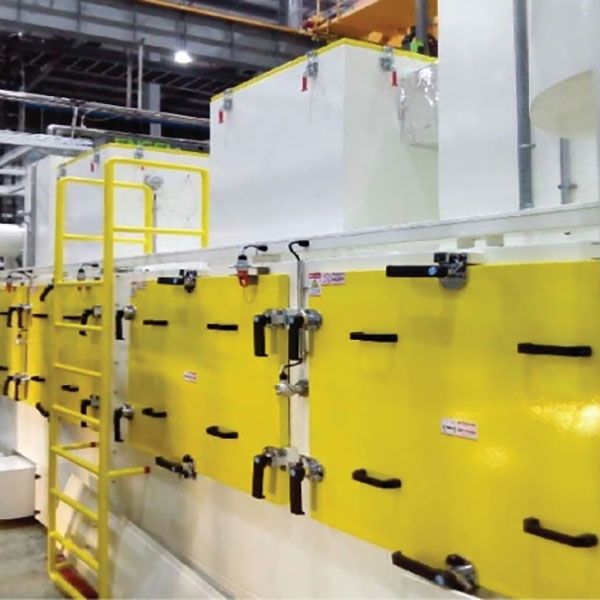
5. Jinway Technology: Leading the Way in Automotive Lighting Annealing Ovens
As a trusted provider of automotive lighting manufacturing solutions, Jinway Technology specializes in designing state-of-the-art annealing ovens that offer:
► Precise temperature control systems for optimal heating and cooling cycles.
► Automated batch processing to enhance production efficiency.
► Customizable settings to accommodate different materials and product designs.
► Energy-efficient designs that reduce operational costs and environmental impact.
► Smart monitoring systems for real-time analysis of annealing conditions.
► High-speed cooling mechanisms to optimize throughput and productivity.
6. Future Innovations in Annealing Technology
► AI-Driven Process Optimization: Machine learning algorithms will further enhance temperature regulation and process control, leading to improved efficiency.
► Eco-Friendly Heating Solutions: Development of low-energy, sustainable heating elements to minimize carbon footprint.
► Integration with Industry 4.0: Smart annealing ovens with IoT connectivity for seamless integration with automated production lines and predictive maintenance features.
7. Conclusion
The annealing process is a crucial step in automotive lighting manufacturing, ensuring that components achieve maximum durability, clarity, and reliability. With the use of advanced annealing ovens, manufacturers can improve product quality, reduce material defects, and optimize production efficiency. Companies like Jinway Technology are at the forefront of this innovation, providing cutting-edge solutions for automotive lighting manufacturers worldwide. By integrating high-quality annealing ovens into the production process, manufacturers can meet industry standards and consumer expectations for superior automotive lighting performance, while also preparing for the future of smart, sustainable manufacturing.